The construction industry is facing plenty of challenges, including identifying bottlenecks and coming up with solutions. Bottlenecks abound in the industry, and they’re only going to get worse without proper intervention.
Construction projects can be complex and challenging, with many different aspects that need to come together in order for the project to be a success. One of the most important factors in any construction project is on-time completion. However, many construction projects face delays due to bottlenecks in the workflow. This blog post will discuss some of the most common bottlenecks and how to prevent them from happening.
5 Common Bottlenecks in Construction Projects
5 Common Bottlenecks in Construction Projects
There are many potential bottlenecks that can occur in construction projects. Some of the most common include:
- Delays in approvals from regulatory bodies
- Lack of skilled labor
- Equipment breakdowns
- Weather conditions
- Material shortages
To prevent these bottlenecks from happening, it is important to be aware of them and have a plan in place to avoid or mitigate them.
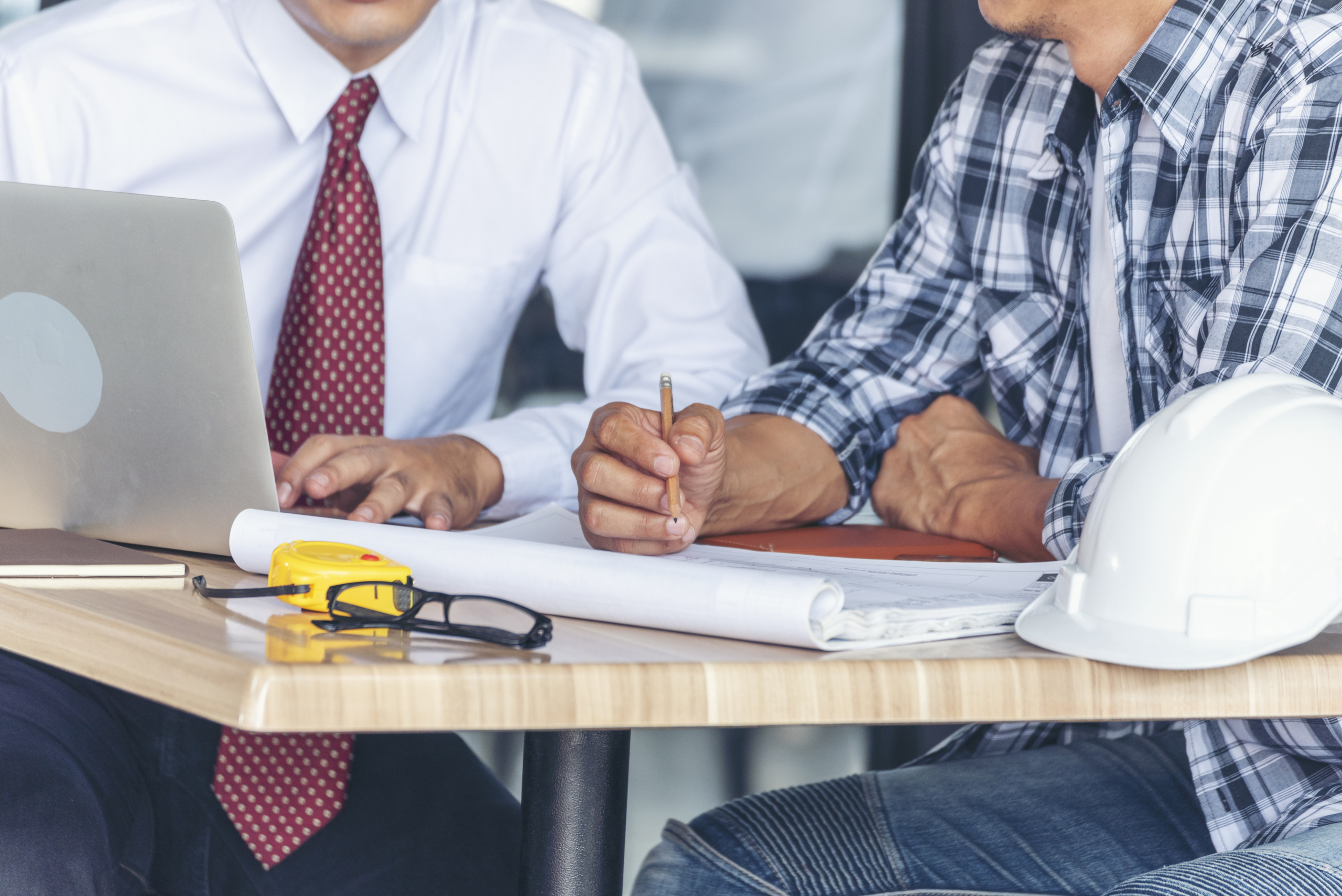
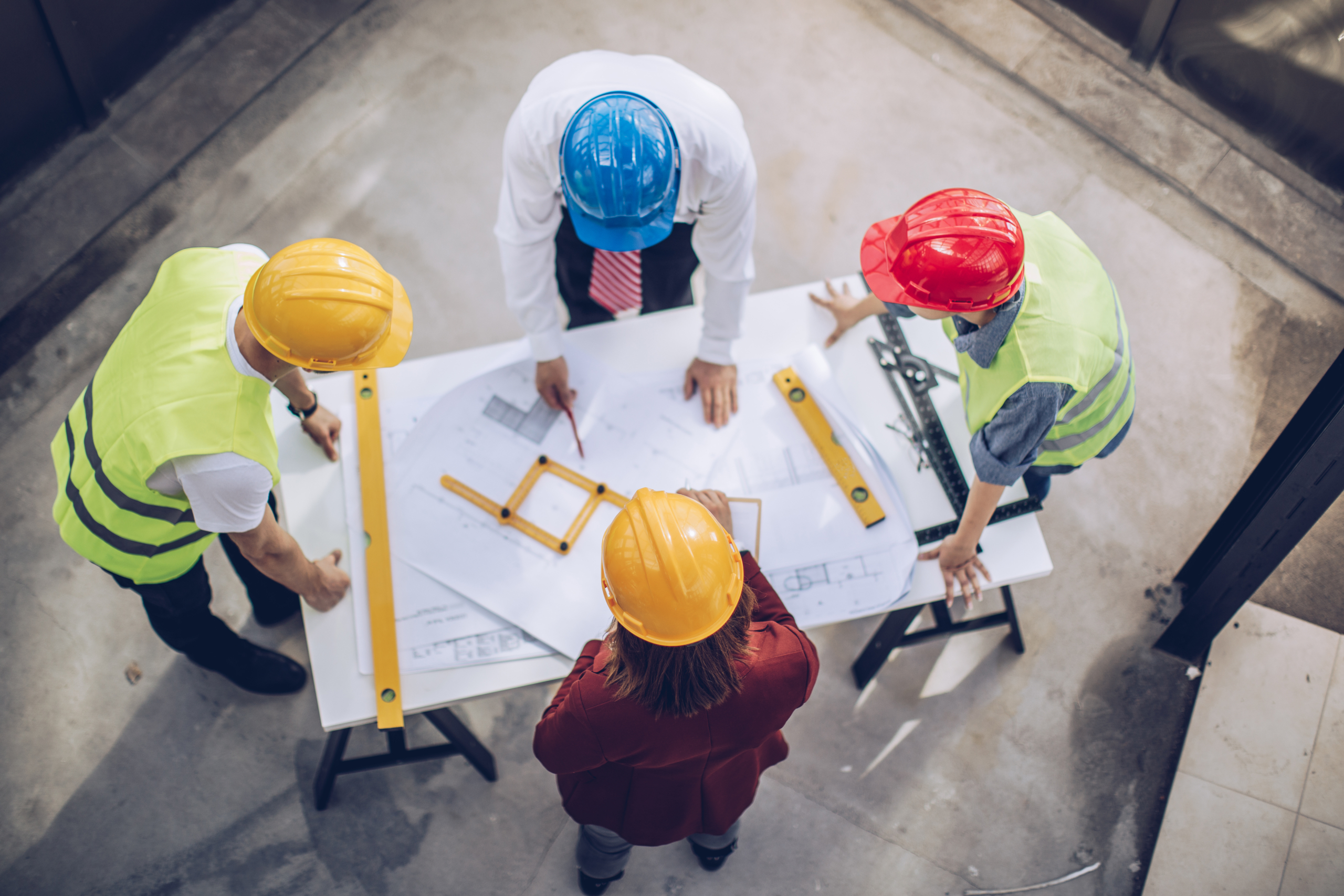
1. Delays in Approvals From Regulatory Bodies
One of the most common bottlenecks in construction projects is delays in approvals from regulatory bodies. This can be a major issue, as it can cause significant delays in the project timeline, especially since it feels like you have no control over what’s happening.
To prevent this bottleneck, you must have a clear and concise plan for the project that includes all required approvals. You may want to also include a buffer to give yourself extra time in case there is a delay. Additionally, it is important to track the status of all approvals and follow up as needed.
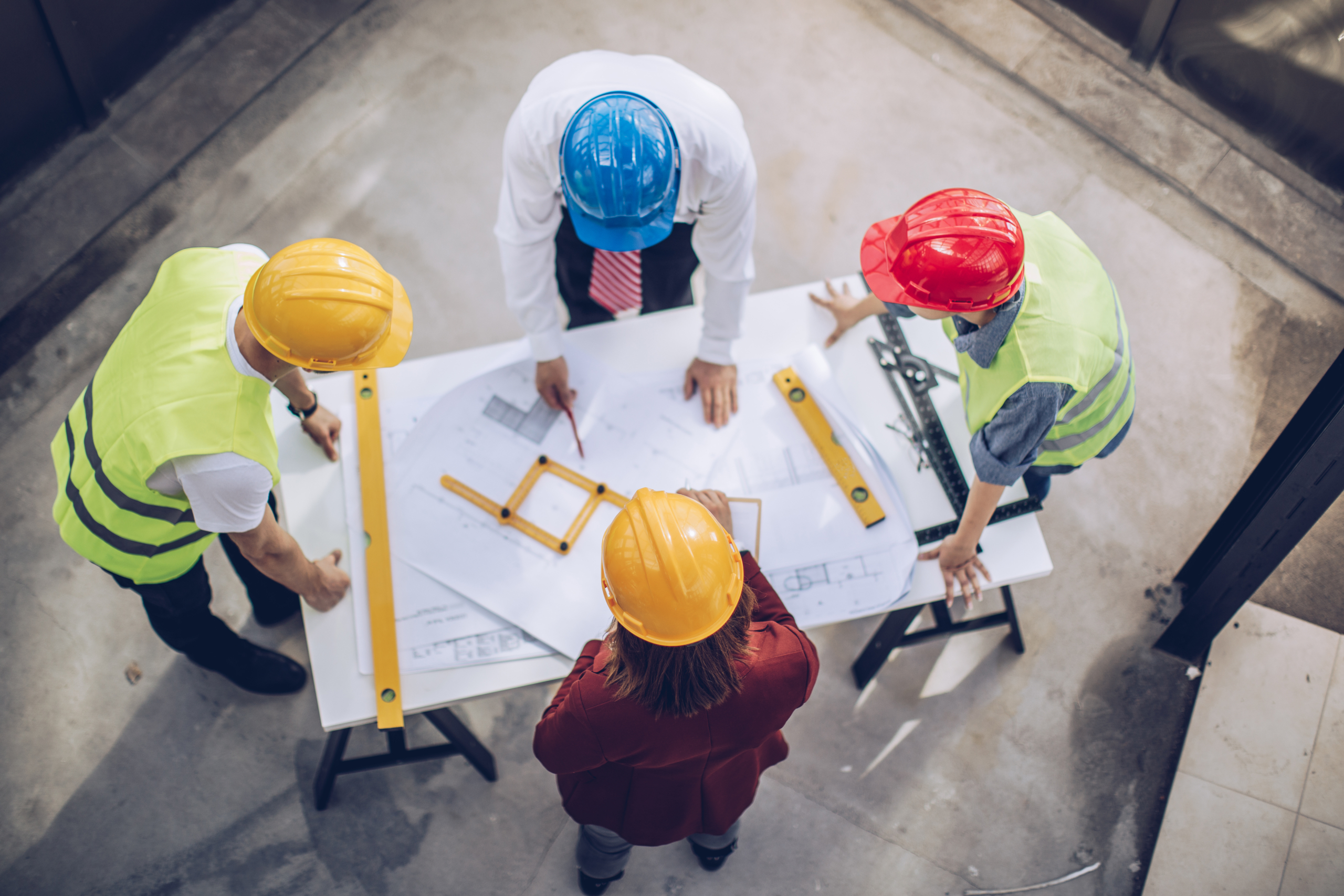
1. Delays in Approvals From Regulatory Bodies
One of the most common bottlenecks in construction projects is delays in approvals from regulatory bodies. This can be a major issue, as it can cause significant delays in the project timeline, especially since it feels like you have no control over what’s happening.
To prevent this bottleneck, you must have a clear and concise plan for the project that includes all required approvals. You may want to also include a buffer to give yourself extra time in case there is a delay. Additionally, it is important to track the status of all approvals and follow up as needed.
2. Lack of Skilled Labor
Attracting skilled labor is a frequent issue that comes up in the construction industry. The result is a major bottleneck. There ends up being not enough workers available to complete the work. A lack of labor is becoming a more frequent issue, as many construction workers are beginning to age out of the workforce with approximately 40% of all workers in construction being between the ages of 45 and 64.
To prevent this bottleneck, it is important to have a clear plan for the project that outlines the necessary skills and experience required for each task. You may also need to be creative in how you attract new and younger workers that have the skills you need. For example, incorporating more robotics or cutting-edge software platforms as part of your daily operations is likely to increase the attraction.
Additionally, it is important to track the availability of skilled labor and have a contingency plan in place in case there are not enough workers available.
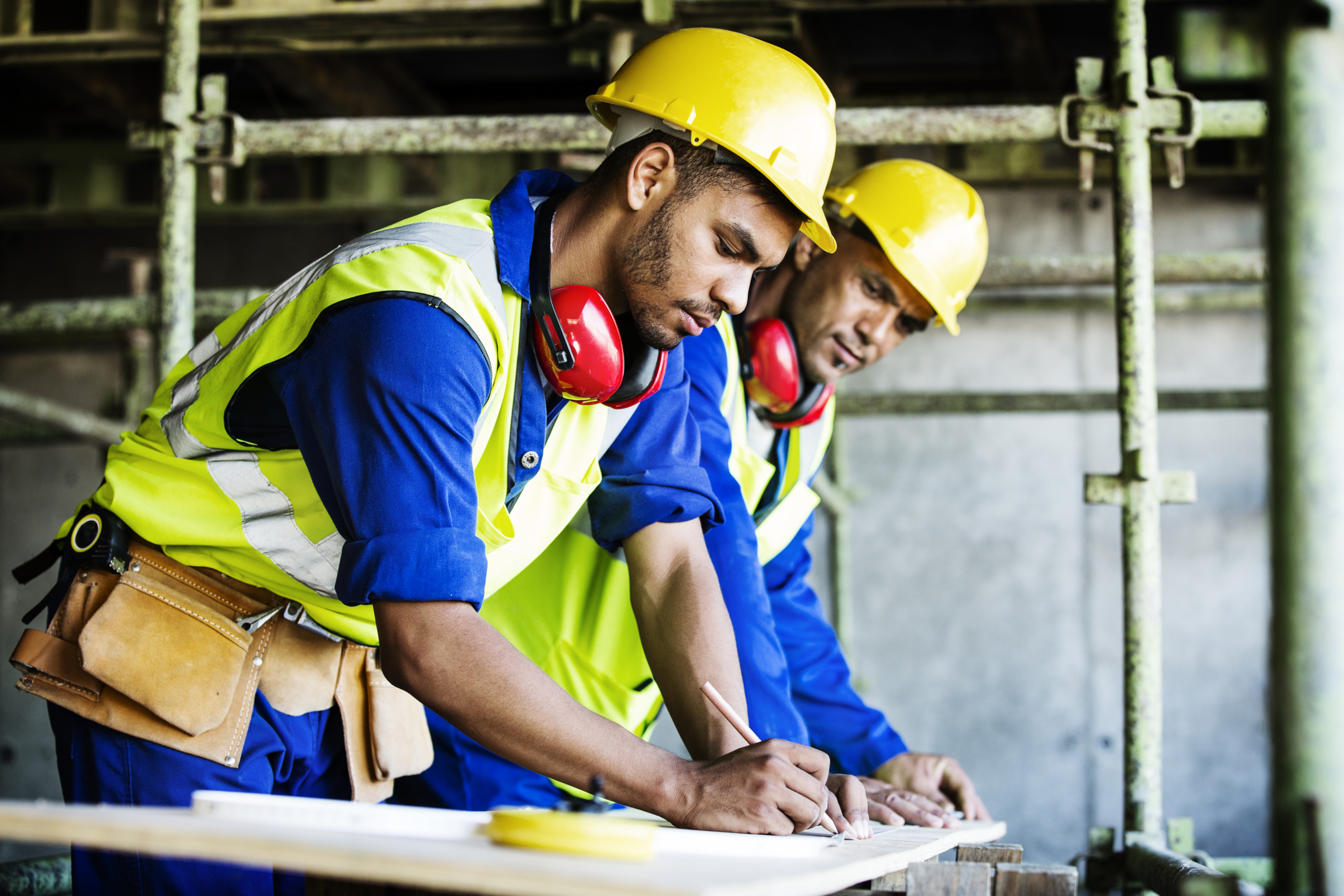
2. Lack of Skilled Labor
Attracting skilled labor is a frequent issue that comes up in the construction industry. The result is a major bottleneck. There ends up being not enough workers available to complete the work. A lack of labor is becoming a more frequent issue, as many construction workers are beginning to age out of the workforce with approximately 40% of all workers in construction being between the ages of 45 and 64.
To prevent this bottleneck, it is important to have a clear plan for the project that outlines the necessary skills and experience required for each task. You may also need to be creative in how you attract new and younger workers that have the skills you need. For example, incorporating more robotics or cutting-edge software platforms as part of your daily operations is likely to increase the attraction.
Additionally, it is important to track the availability of skilled labor and have a contingency plan in place in case there are not enough workers available.
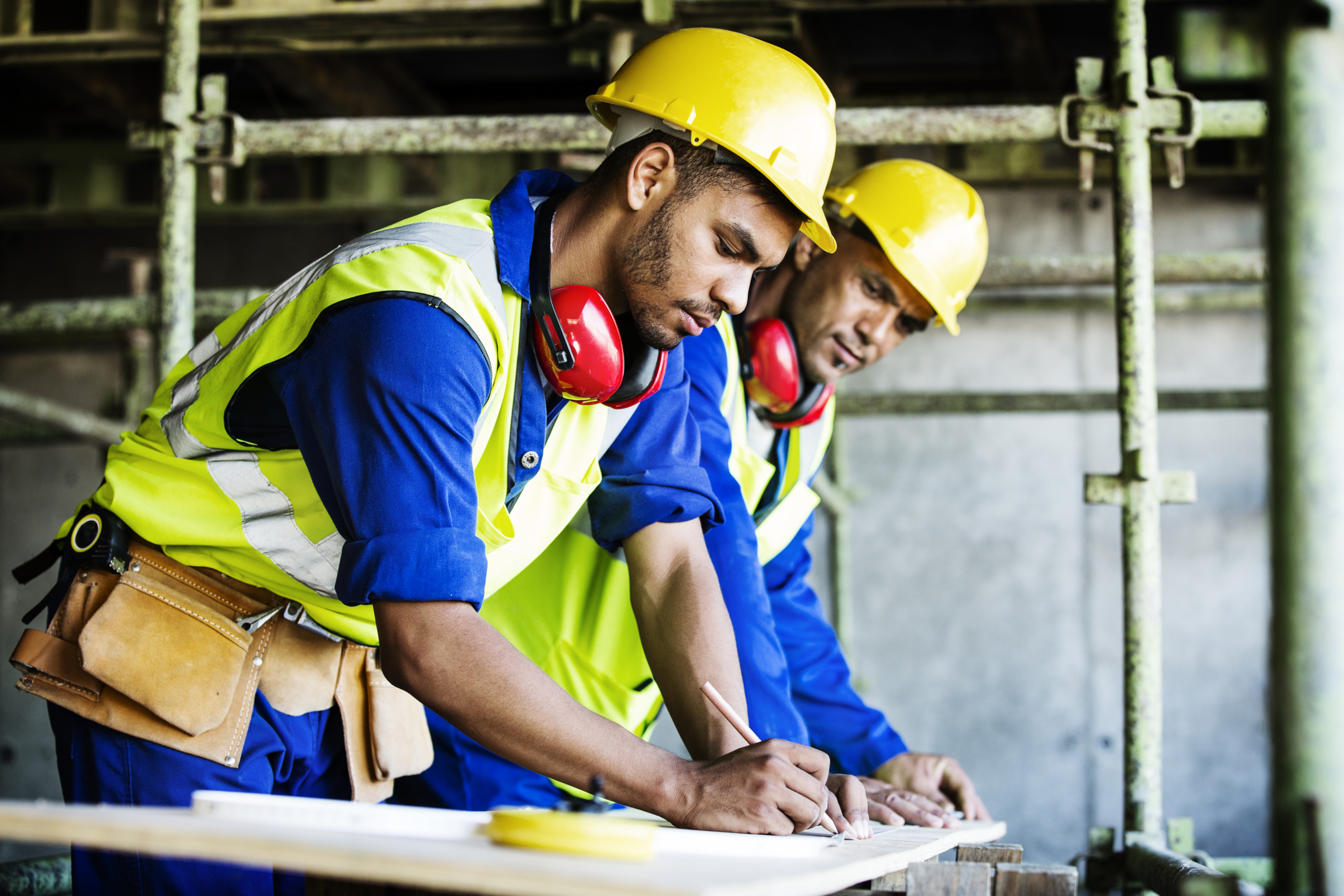
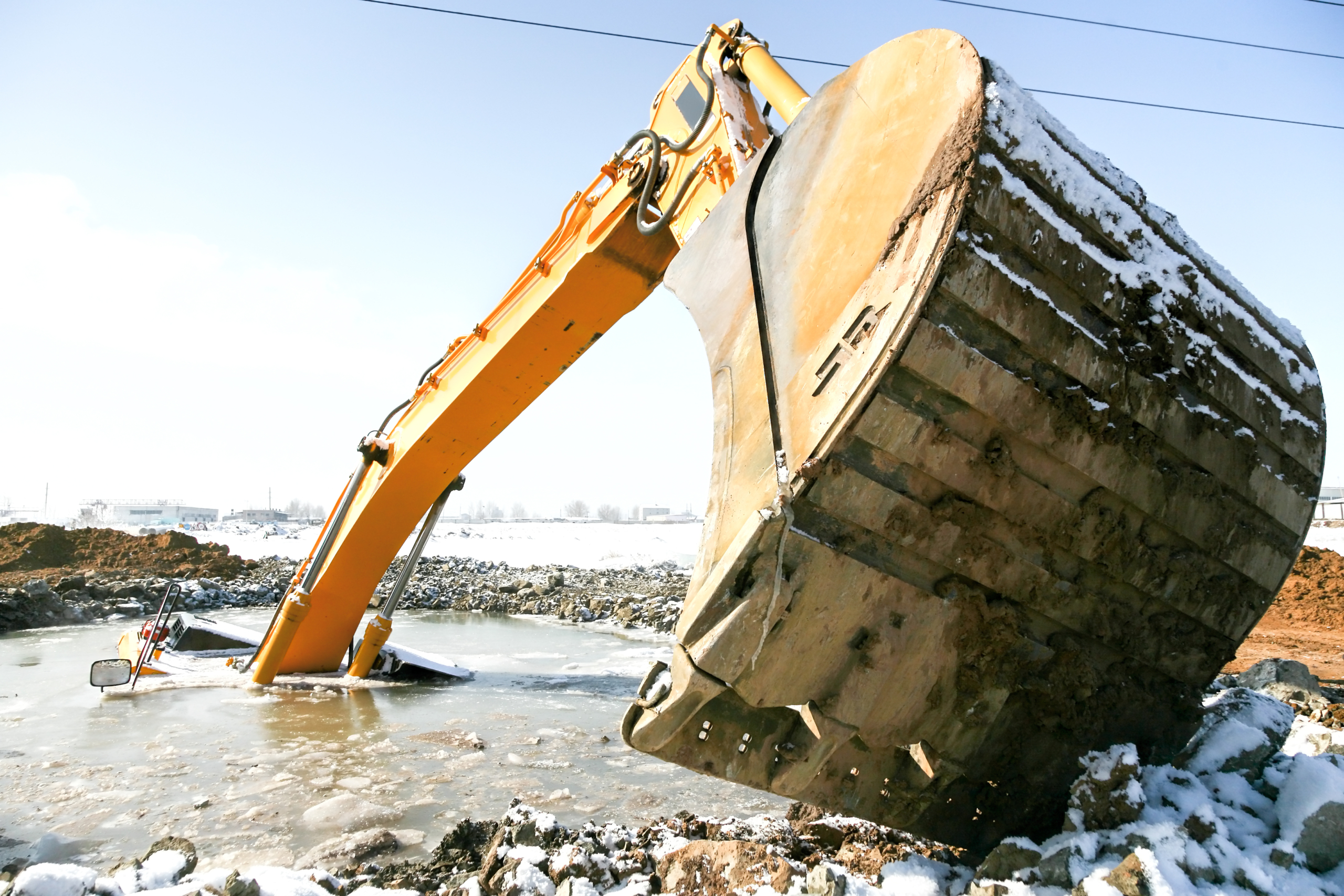
3. Equipment Breakdowns
3. Equipment Breakdowns
Another potential bottleneck occurs when equipment breaks down, as it can cause significant delays in the project timeline. The last thing you need is having a major piece of equipment breakdown while not being prepared.
To prevent this bottleneck from happening, it is important to have a maintenance plan in place for all equipment. Additionally, it is important to have a backup plan in place in case of an equipment failure.
4. Weather Conditions
Weather conditions can also be another potential bottleneck in construction projects. Weather is notorious for causing delays in the overall timeline. To prevent this bottleneck from happening, it is important to have a plan in place for all possible weather conditions. Monitoring the weather and quickly communicating severe conditions is critical to mitigating bottlenecks before they happen.
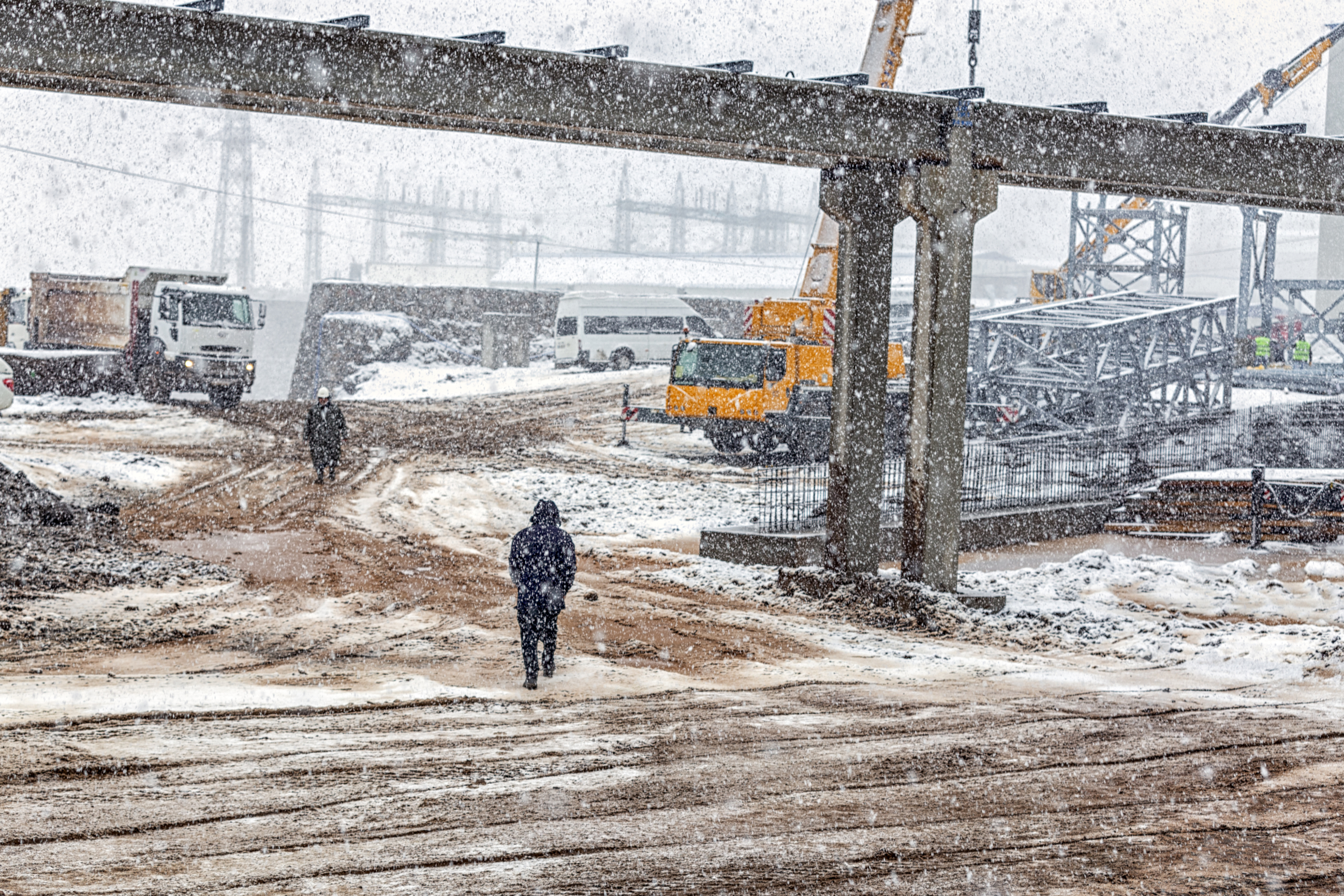
4. Weather Conditions
Weather conditions can also be another potential bottleneck in construction projects. Weather is notorious for causing delays in the overall timeline. To prevent this bottleneck from happening, it is important to have a plan in place for all possible weather conditions. Monitoring the weather and quickly communicating severe conditions is critical to mitigating bottlenecks before they happen.
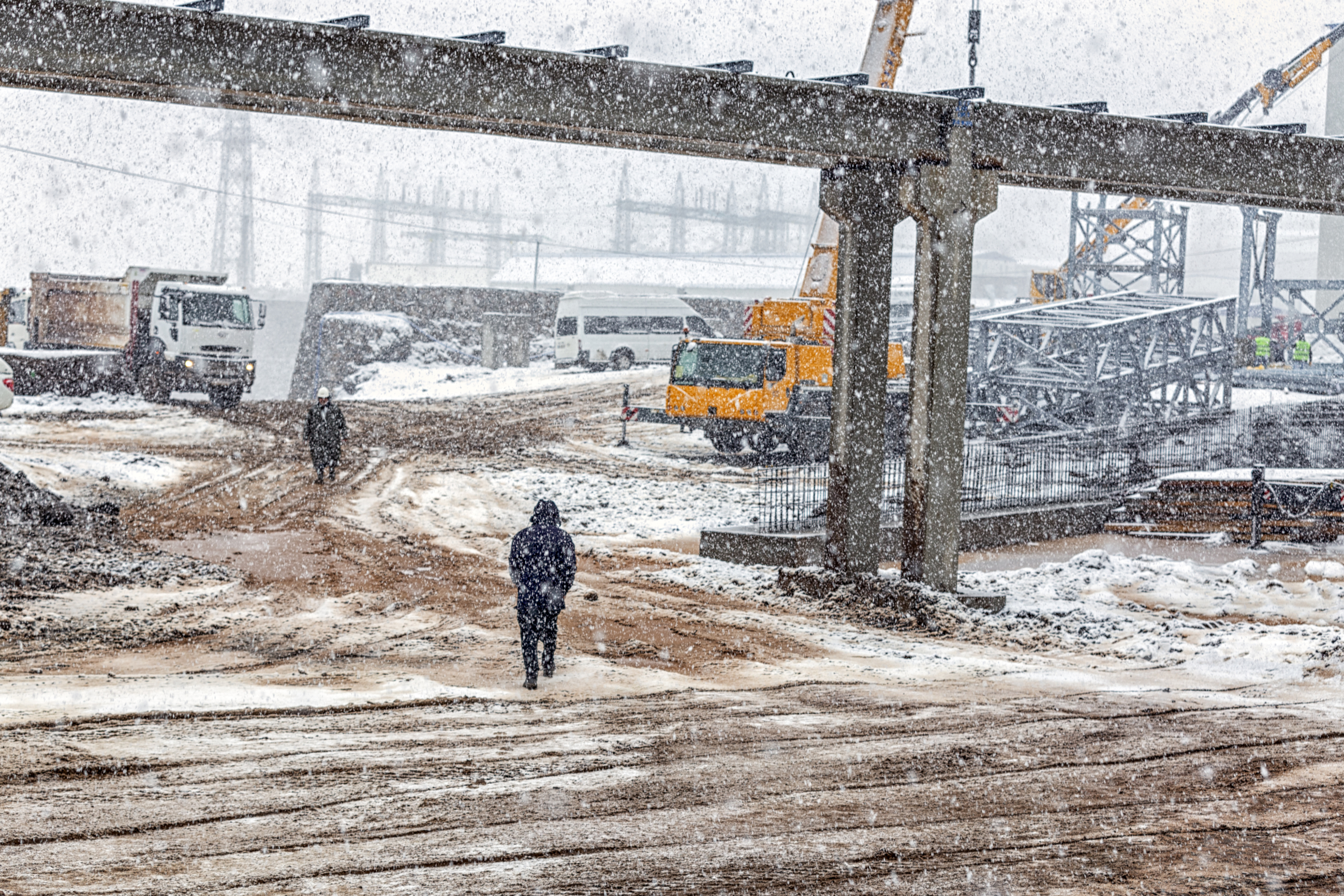
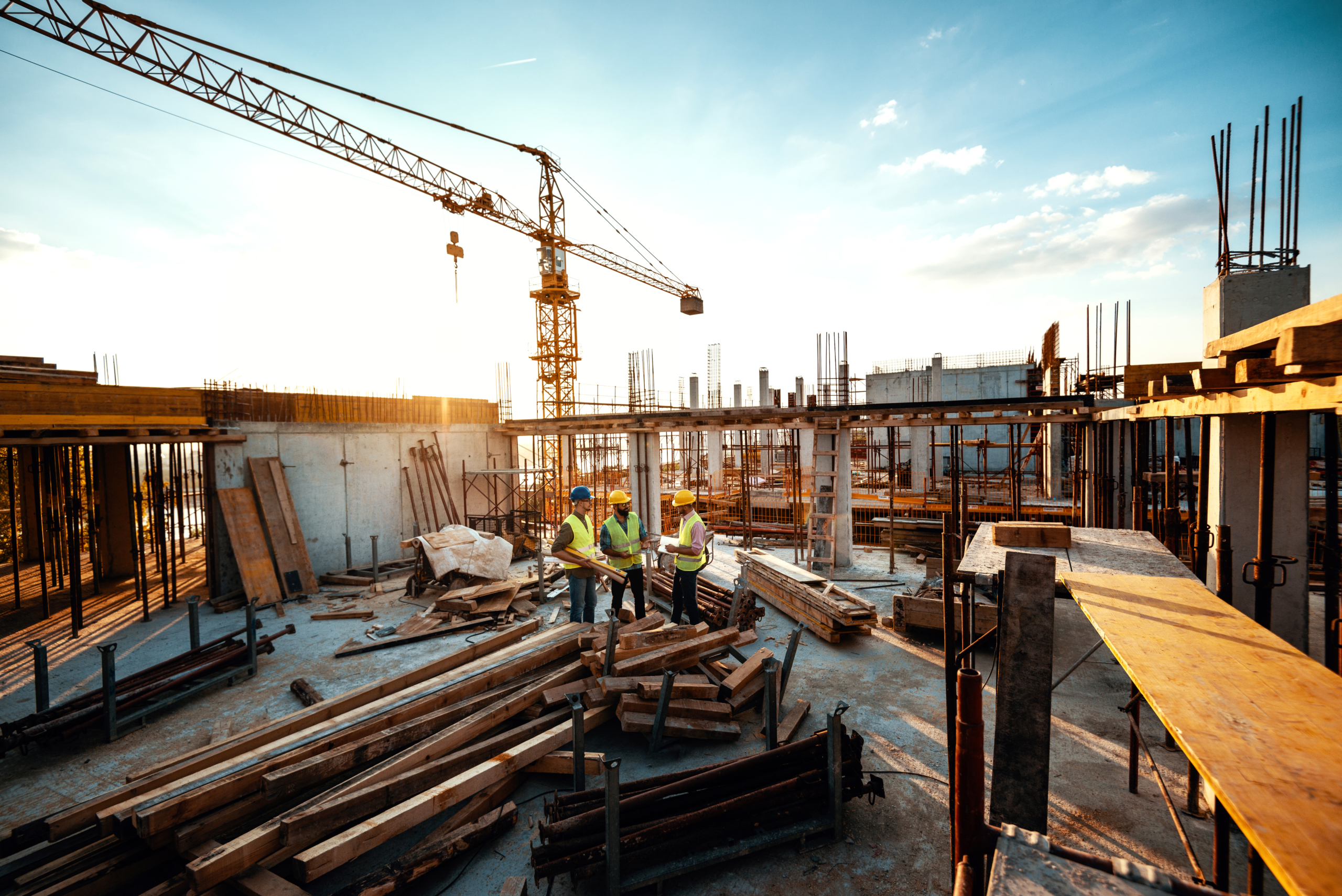
5. Material Shortages
5. Material Shortages
Weather conditions can also be
You may also face material shortages which can result in a bottleneck issue. If shortages aren’t considered, you can end up with delays in the project timeline. This one is a little trickier to prevent, given the current worldwide shortages.
To help prevent this bottleneck from happening, it is important to have a plan in place for all possible material shortages. This might include having multiple vendors you can contact for the supplies you need if you experience a shortage.
6 Other Steps You Can Take to Prevent Bottlenecks
6 Other Steps You Can Take to Prevent Bottlenecks
In addition to the steps listed above, there are a few other things you can do to prevent bottlenecks in construction projects. After all, the more you can prevent delays, the more efficiently your construction projects will be completed, leading to happier customers.
1. Implementing Risk Management
1. Implementing Risk Management
By identifying and assessing risks, you can develop a plan to mitigate them.
Once risks have been assessed, it’s critical to have a workflow that will ensure your employees know what to do in the event of unforeseen problems or circumstances. This will help to ensure that potential bottlenecks are avoided or minimized.
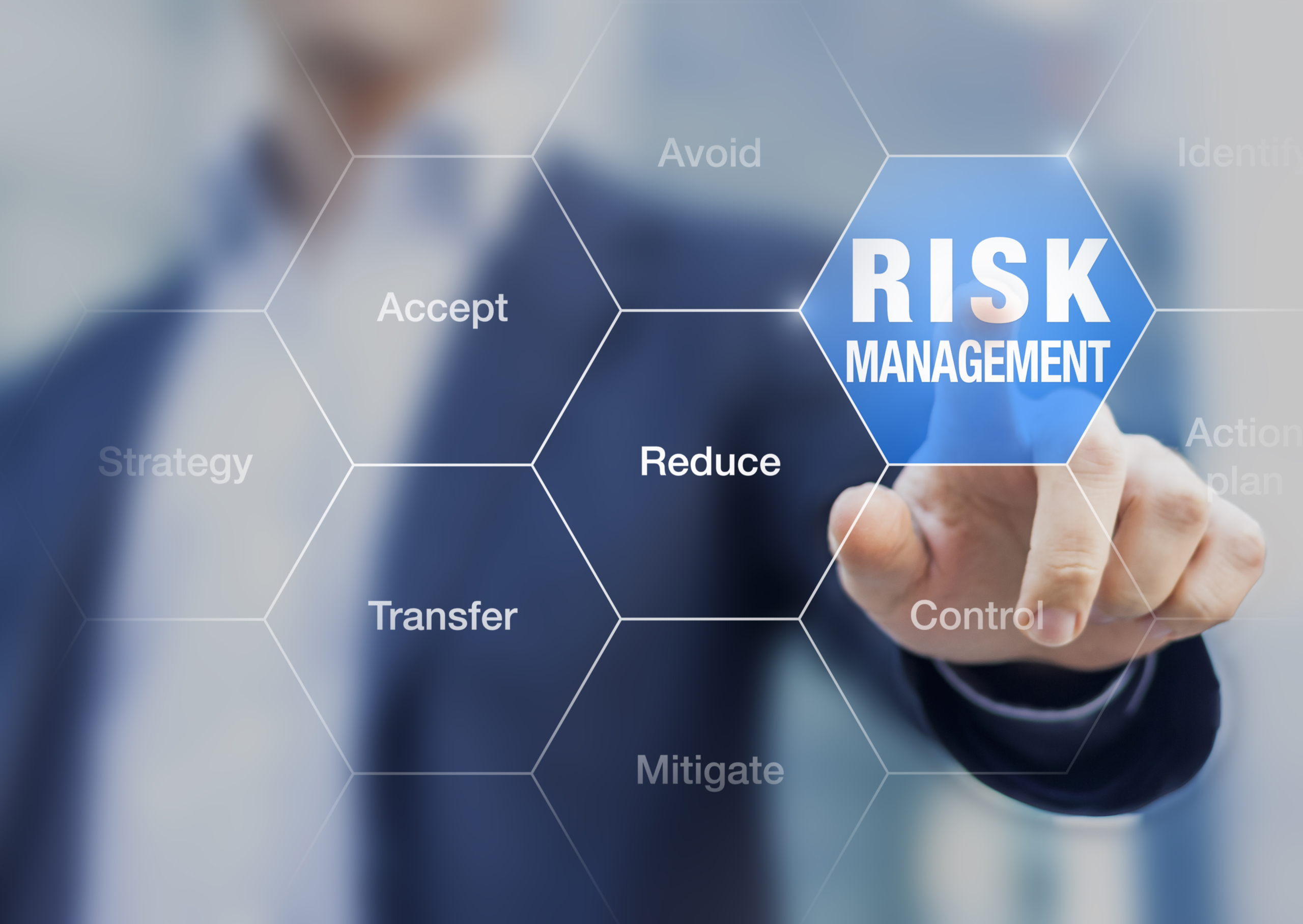
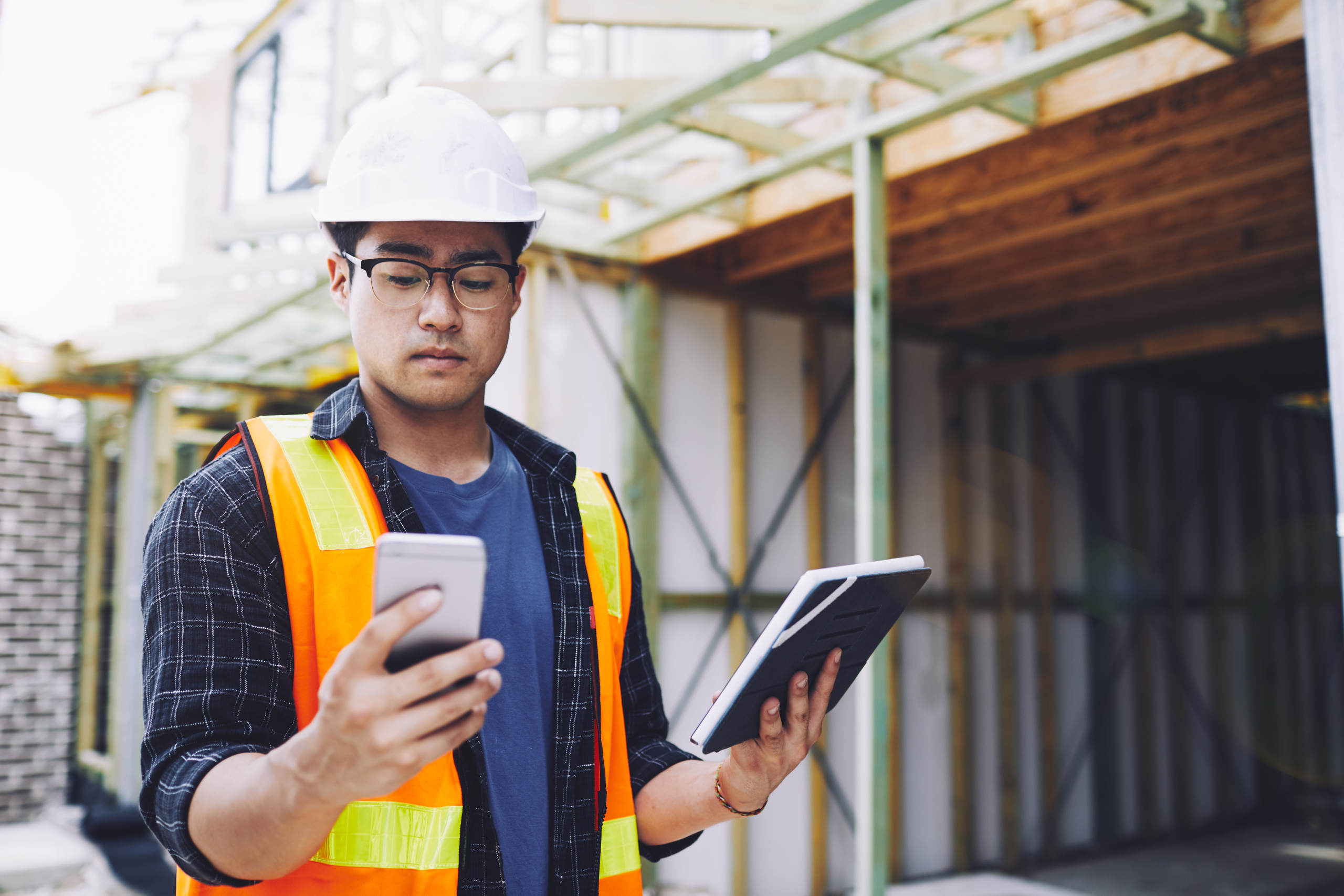
2. Improving Communication
Communication is critical in construction projects, as it helps to ensure that everyone is on the same page.
By improving communication, you can avoid misunderstandings and miscommunication that can lead to bottlenecks. One way you can improve communication is to have a single platform where everyone can communicate, like the one found at GLXY Software Solutions.
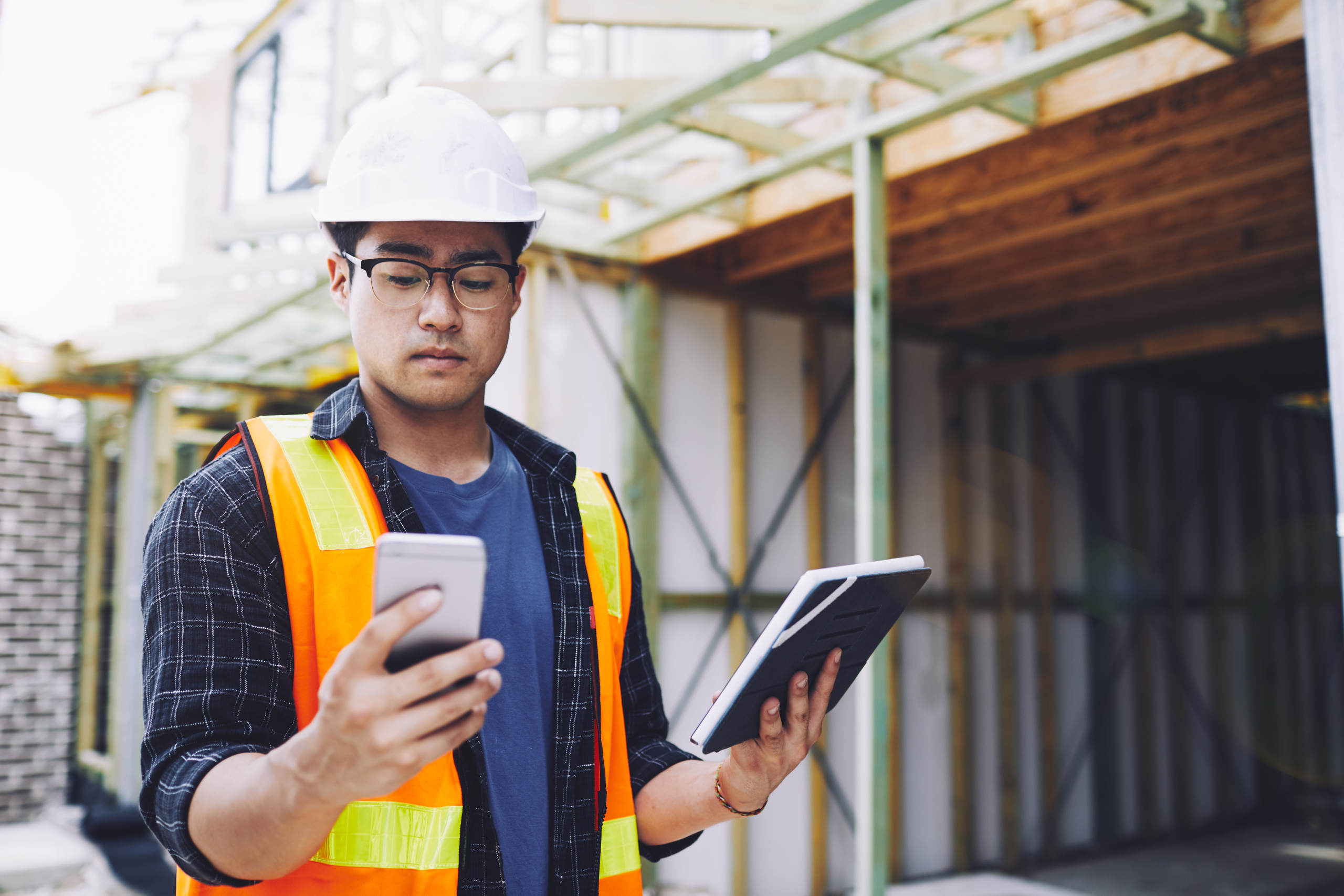
2. Improving Communication
Communication is critical in construction projects, as it helps to ensure that everyone is on the same page.
By improving communication, you can avoid misunderstandings and miscommunication that can lead to bottlenecks. One way you can improve communication is to have a single platform where everyone can communicate, like the one found at GLXY Software Solutions.
3. Improving Planning
3. Improving Planning
Another way to prevent bottlenecks in construction projects is to improve planning. Planning is critical in construction projects, as it helps to ensure that all aspects of the project are taken into account. You can improve planning by:
- Adding time buffers
- Having second- and third-choice vendors
- Proactively and continuously monitoring for risks
- Being as communicative as possible with vendors, subcontractors, and workers
- Get input from all participants
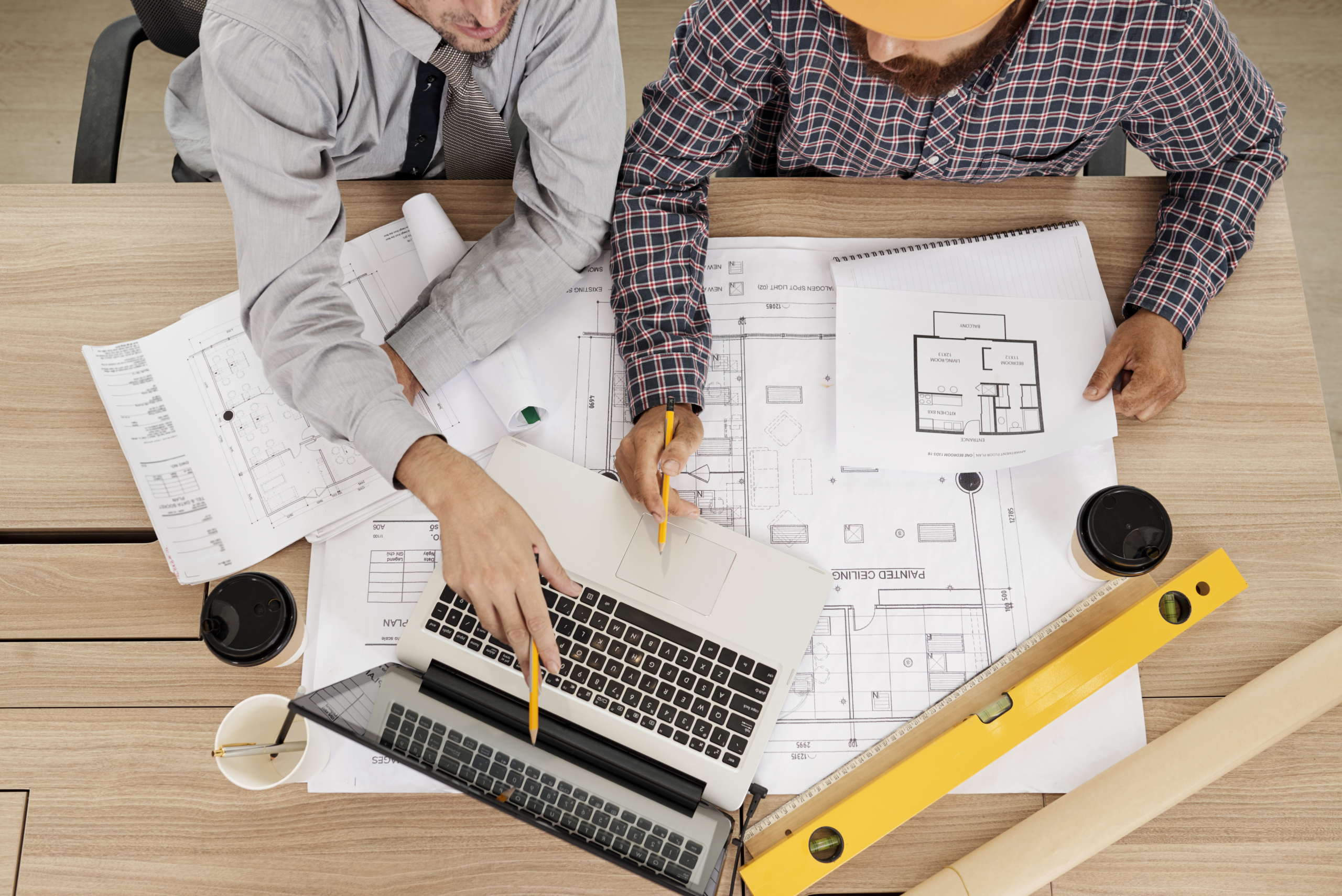

4. Excellent Labor Management
Excellent labor management can also help avoid bottlenecks in construction projects. By managing labor effectively, you can ensure that all workers are utilized efficiently, even if you have fewer workers than you’d like.
Knowing what skills are available also lets you know what kind of training or upskilling would be useful for your workers. You may also discover that you may need to hire someone with a specific skill set that is otherwise missing.

4. Excellent Labor Management
Excellent labor management can also help avoid bottlenecks in construction projects. By managing labor effectively, you can ensure that all workers are utilized efficiently, even if you have fewer workers than you’d like.
Knowing what skills are available also lets you know what kind of training or upskilling would be useful for your workers. You may also discover that you may need to hire someone with a specific skill set that is otherwise missing.
5. Having the Right Equipment
5. Having the Right Equipment
Another way to prevent bottlenecks in construction projects is to have the right equipment. Having the right equipment helps to ensure that all tasks can be completed efficiently and without delays.
Many times, tight budgets can lead to cost-cutting, and high-quality equipment can be the first thing to go. The truth is that not having the right equipment can lead to serious consequences ranging from poor finished quality to accidents involving workers. You should always ensure that the right equipment is available to minimize risk and to maintain high-quality standards.
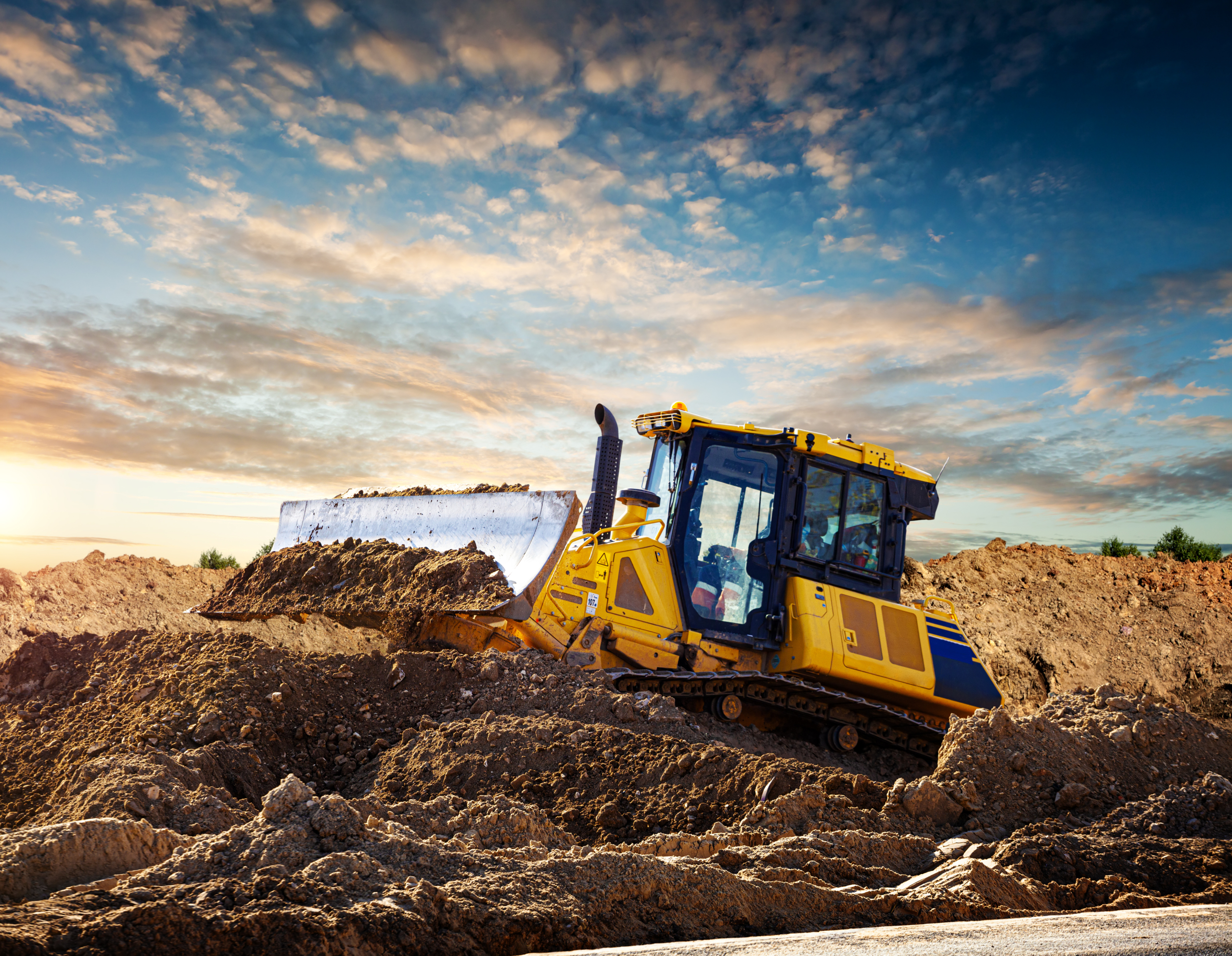
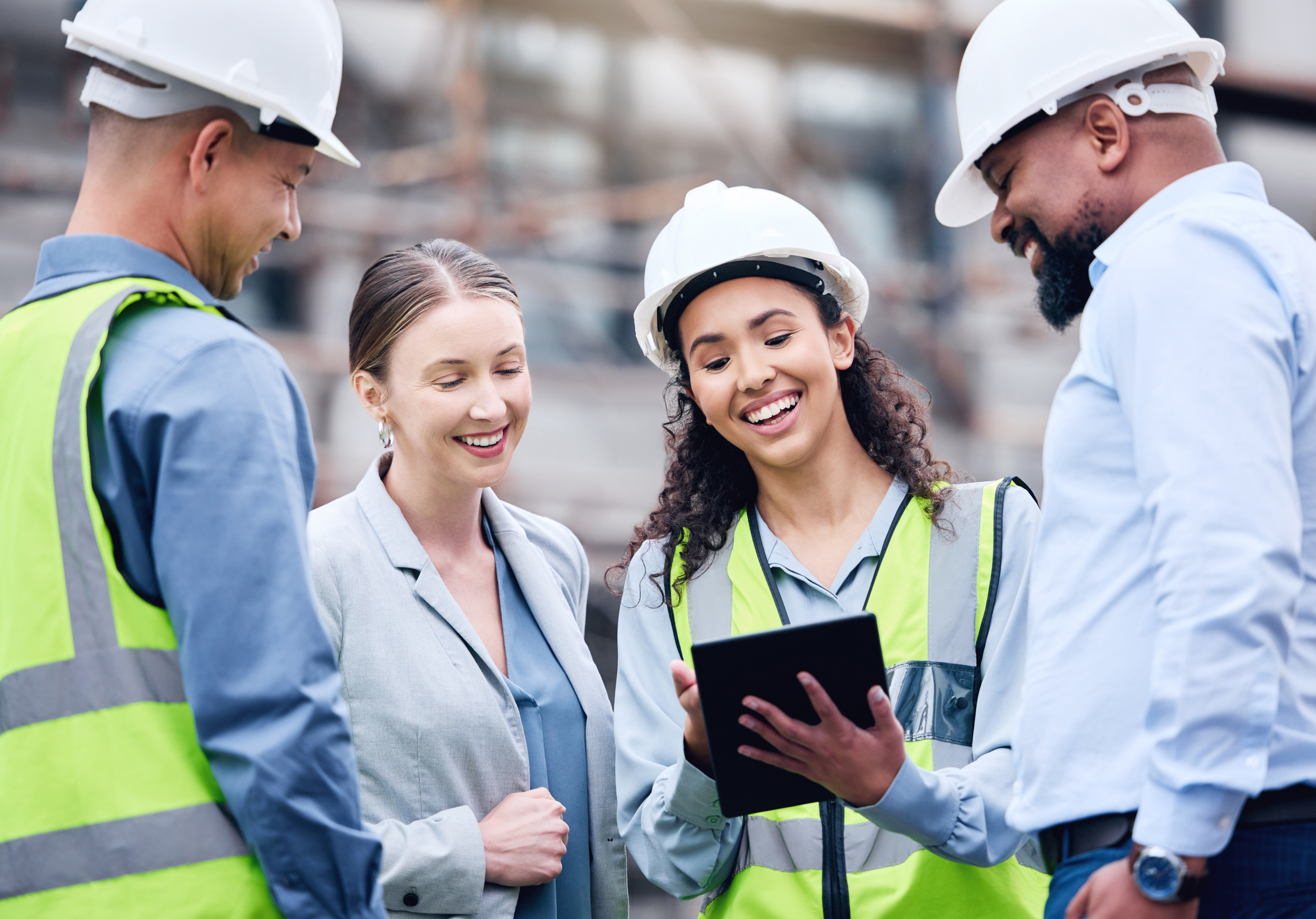
6. Physical Space Management
Last but not least, another way to prevent bottlenecks in construction projects is to manage physical space effectively. Space management refers to site congestion, access obstructions, and anything else that physically keeps your workers from getting the job done.
To keep space management up and running, you want to continuously evaluate spatial issues to minimize any factors that could otherwise hurt your workflow. By managing physical space, you can ensure that all workers have the necessary room to work and that there are no delays due to a lack thereof.
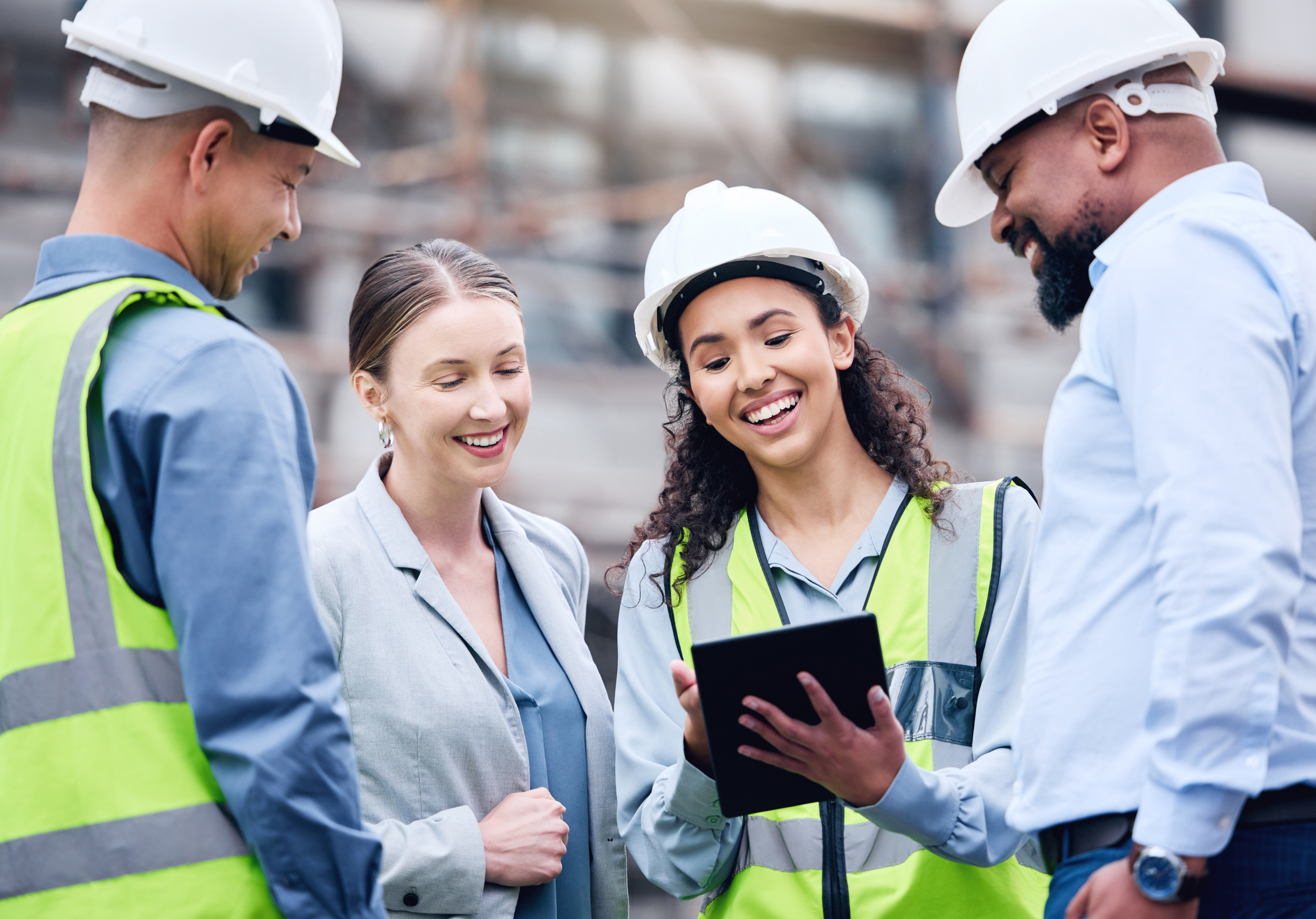
6. Physical Space Management
Last but not least, another way to prevent bottlenecks in construction projects is to manage physical space effectively. Space management refers to site congestion, access obstructions, and anything else that physically keeps your workers from getting the job done.
To keep space management up and running, you want to continuously evaluate spatial issues to minimize any factors that could otherwise hurt your workflow. By managing physical space, you can ensure that all workers have the necessary room to work and that there are no delays due to a lack thereof.
Bottom Line
There are many potential bottlenecks in construction projects. However, by applying the tips listed above, you can help to avoid or minimize them. By doing so, you can help to ensure that your construction project is a success.
If you’d like to see what GLXY Software Solutions can do to help you improve bottlenecks in current or future project workflows, let us know.